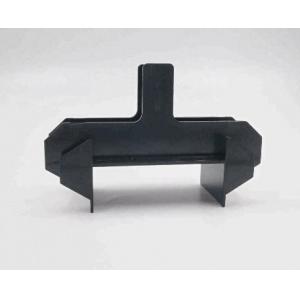
Add to Cart
Машина впрыски ПВК ПП АБС ПК разделяет просвечивающее изготовленной на заказ крышки УЛЬТРАФИОЛЕТОВОЕ стабилизированное
Первый шаг получать пластиковую впрыску части отлитый в форму иметь модель (CAD) компьютерного проектирования части произведенной инженером по дизайну. Трехмерная (3Д) модель КАД после этого идет к компании инжекционного метода литья где создатель прессформы (или тоолмакер) сделают прессформу (инструмент) которая будет помещена в машина инжекционного метода литья для того чтобы сделать части.
Прессформы точност-подвергаются механической обработке обычно от стали или алюминия, и могут стать довольно сложными в зависимости от дизайна части. Пластиковые материалы сжимают на различных тарифах когда они охлаждают, поэтому прессформа должна быть построена с рассмотрением для тарифа усушки материала будучи использованной для частей. Другими словами, формула приложена в конструкции прессформы небольшого для увеличения размера так как когда пластиковая усушка произойдет, часть будет к габаритным спецификациям модели КАД.
О инжекционном методе литья
Инжекционный метод литья самый общий современный метод частей пластмассы производства. Он использован для создания разнообразие частей с различными формами и размерами, и идеально для произведения высоких уровней такой же пластиковой части. Инжекционный метод литья широко использован для изготовлять разнообразие части, от самого небольшого компонента медицинской службы ко всем панелям тела автомобилей. Процесс производства для произведения пластиковых частей и от термопластиковых и термореактивных материалов, инжекционного метода литья может создать части с сложной геометрией которая много других процессов не могут.
Пластиковый инжекционный метод литья процесс производства где смола в бочонке нагрета к жидкому государству, тогда съемка в прессформу формирует часть в форме прессформы. Смола начинает как пластиковые лепешки, которые сила тяжести кормить в машину инжекционного метода литья через воронкообразный хоппер. Лепешки кормятся от хоппера в хэатед камеру вызванную бочонок где они расплавлены, обжаты, и впрыснуты в систему бегуна прессформы ресипрокатинг винтом.
По мере того как зерна медленно двинуты вперед типа винт плунжером, расплавленная пластмасса принуждается до сопло которое усаживает против втулки спруэ прессформы, позволяющ ей войти полость прессформы через систему ворот и бегуна. Часть отлитая в форму впрыской остается на установленной температуре поэтому пластмасса может затвердеть почти как только прессформа заполнена.
Часть охлаждает и твердеет к форме полости прессформы. После этого 2 половины прессформы (полость или сторона «а» и ядр или сторона «б») раскрывают вверх и выталкивающие шпильки нажимают часть из прессформы куда она падает в ящик. После этого половины прессформы закрывают назад совместно и процесс начинает снова для следующей части.
Стальная прессформа впрыски
Прессформы впрыски, или тоолинг прессформы, сформированные половины которым приведенный совместно в машину инжекционного метода литья, который нужно заполнить с жидкой пластмассой и произведите пластиковые части в их изображении. Сторона полости, или сторона «а», типично половина которая сформирует поверхность «самое лучшее» части, и сторона ядра, или сторона «б», типично покажет визуальные несовершенства причиненные выталкивающими шпильками потому что части получают выкинутыми от этой половины.
Прессформы впрыски изготовлены путем подвергать механической обработке или электрической разрядкой подвергая (EDM) механической обработке. Стандартный подвергать механической обработке был традиционным методом прессформ впрыски здания с мельницей колена. Технология выдвинула процесс, и подвергать механической обработке (CNC) численным управлением компьютера стал прессформами преобладающего способа изготовления сложными, с более точными деталями, и в меньше времени чем традиционный метод.
ЭДМ процесс в котором форменное, медное или графитовый электрод медленно понижены на поверхность прессформы, которая погружена в масле парафина. Электрическое напряжение тока приложенное между инструментом и размыванием искры причин прессформы прессформы отделывает поверхность в обратной форме электрода. ЭДМ было широко используемым в делать прессформы - много компаний прессформы впрыски теперь имеют ЭДМ внутреннее. Процесс позволяет образованию прессформ которые трудны для того чтобы подвергнуть механической обработке, как те с особенностями как нервюры или квадратные углы. Он позволяет пре-затвердетым стальным изложницам быть сформированным без требования термической обработки.
Сравненный к другим пластиковым процессам производства как подвергать механической обработке КНК или печатание 3Д, инжекционный метод литья имеет высокий вверх-передний вклад потому что дорого стоит тоолинг. Однако, для больших выпусков продукции тысяч или даже миллионов идентичных частей, инжекционный метод литья типично более менее дорог в конечном счете, несмотря на высокий начальный вклад тоолинг, из-за более низкой поштучной платы на высоких уровнях. К тому же, гораздо быстрее процесс производства чем упомянутые другие.
Прессформы можно сделать из пре-затвердетой стали, стали которая затвердета после того как прессформа произведена, алюминий, и/или сплав берилли-меди. Выбор материала прессформы определен в части числом частей, который нужно произвести.
Множественн-полость отливает в форму (прессформы семьи)
Части отлитые в форму семьей
В дополнение к одиночной пластиковой части будучи произведенной в цикле прессформы, прессформу можно также конструировать для произведения множественных номеров такой же части в единственном выстреле. Инструмент с одним впечатлением часто вызван одиночной прессформой впечатления (полости), тогда как изготовленная на заказ прессформа впрыски с двумя или больше полостями такой же части названа множественная прессформа впечатления (полости). Число впечатлений в прессформе часто неправильно названо кавитация. Некоторые весьма высокообъемные прессформы – как те для крышек бутылки – могут иметь над 128 полостями.
Множественная прессформа впечатления (полости) может также быть названа прессформа «семьи». Однако, прессформа семьи более точно определена как одно которое может произвести множественные, размером с как части в таком же количестве, цвет и материал. Части отлитые в форму семьей часто часть собрания, как сопрягая верхняя половина и половина дна.
Пример Овермолдинг
Овермолдинг пластиковый процесс инжекционного метода литья который очень полезен для произведения частей мульти-материала с некоторыми уникальными свойствами. Например, этот процесс можно использовать для добавления второй части, различного материала, для ручки или сжатия. Изобразите электрический инструмент с сжатием сделанным из более мягкого материала чем тело инструмента. Подобно, регулятор игры можно изготовить с различными текстурами пластмасс на теле его.
По существу, ранее часть отлитая в форму впрыской одного материала (субстрата) ре-введена в машину инжекционного метода литья, и различный материал (овермолд) впрыснута для того чтобы сформировать новый слой над первой частью.
Некоторые специализированные машины инжекционного метода литья имеют два или больше блоки впрыски которые могут «овермолд» в одиночном цикле прессформы. Например, «двухразовый,» или «многоразовые» прессформы впрыски сперва отливают основную форму в форму в низкопробном цвете пластикового материала, тогда второй материал, другого цвета, впрыснут в остальные открытые пространства для произведения цельного, часть пластмассы мульти-цвета.
Овермолдинг как не прямодушно как инжекционный метод литья часть из одиночного материала, и оно нет без своих ограничений. Одно рассмотрение что 2 материала должны быть совместимы, химически и термально. В виду того что пластиковые материалы имеют различные температуры мельт, материал субстрата должен иметь более высокую температуру мельт чем овермолдинг материал, в противном случае первоначальная часть расплавила бы и деформировала бы когда овермолдинг материал впрыснут.
Части металла, керамических или пластиковых можно ввести в жидкое термопластиковое к мульти-материалу формы, крепкие части с дополнительной функциональностью. Например, продетые нитку вставки металла можно отлить в форму в части для того чтобы позволить им быть прикрепленным в другие части.
Прессформа вставки может уменьшить цену путем врезать вторичные части в пластиковый процесс инжекционного метода литья, в отличие от установки частей после отливать в форму. Путем интегрировать вставки во время прессформы, части будут крепкими сравненные к укреплять части в пост-прессформе. Конечно, части вставки должны мочь выдержать высокую температуру и давление процесса инжекционного метода литья.
Прессформа вставки естественно более сложный процесс который стандартному инжекционному методу литья, поэтому некоторые компании инжекционного метода литья больше испытывают в процессе чем другие. Для выпусков продукции низко-тома, оператор машины может нагрузить вставки в прессформу вручную, до пластикового цикла впрыски. Для высокообъемных выпусков продукции, однако, он общий для использования автоматизированного машинного оборудования установить вставки в прессформу.
Последовательность событий во время производства вызвана цикл. Она начинает когда прессформа закрывает и полимер впрыснут в полость прессформы. Когда полость заполняет, прессформа поддерживает держа давление определить материальную усушку.
После этого, винт поворачивает, и следующая съемка двигает к фронту винта. Это причиняет винт прореагировать, и, как только охлаженный, прессформа раскрывает и пластиковая извлекли часть, который.
Формулу можно использовать для того чтобы определить время цикла инжекционного метода литья. Время оно принимает для того чтобы сделать часть используя инжекционный метод литья высчитано как:
Полное время = 2М + т + к + е
Где:
(2М) = дважды прессформа открытая/время закрытия
(Т) = время впрыски (С/Ф)
(К) = время остывания
(Э) = время отстрела (е)
(С) = размер прессформы (ин3)
(Ф) = расход потока (ин3/минута)
Части заключения и отстрела прессформы отлитые в форму продолжительностями впрыска могут продолжать от чем секунда к немного минут, в зависимости от размера прессформы и машины. Время остывания, которое преобладает процесс, зависит от максимальной толщины части.
Оптимизировать процесс инжекционного метода литья необходим потому что оно влияет на цену, качество, и урожайность. Некоторые из различных проверок оптимизирования включают:
• Оптимизируйте время пребывания путем проводить исследования замораживания уплотнения ворот или ворот
• Проводите исследование времени остывания для того чтобы оптимизировать время остывания для части отлитой в форму впрыской
• Исследования падения давления определяют если машина имеет достаточное давление двинуть винт на установленный тариф
• Выполните кривые выкостности для того чтобы определить скорости впрыски
• Поменяйте температуры мельт и давления удержания оптимизировать отростчатое окно
Когда работа инжекционного метода литья настраивается в первый раз и размер съемки для этой прессформы неизвестен, проба прессформы будет проведена для того чтобы получить все «набранный внутри.» Техник прессформы обычно будет начинать с небольшим весом съемки и будет заполнять прессформу постепенно до тех пор пока он не будет 95 до 99% полные. После этого небольшое количество удержания давления приложено, и время пребывания увеличено до тех пор пока замораживание ворот (время затвердевания) не будет происходить на части отлитой в форму впрыской. Затвердевание ворот важно потому что оно определяет время цикла, и время цикла критический определитель в эффективности, и поэтому экономике, производственного процесса. Если части имеют метки раковины, то держа давление будет увеличено до тех пор пока они не будут уменьшены и вес части достиган. Как только установки установлены внутри и машина инжекционного метода литья делает интересные отрывки из книг, лист установки произведен для унифицировать процесс для будущих выпусков продукции.